The aviation industry has always been at the forefront of technological advancements, constantly pushing the boundaries of what is possible in terms of design, materials, and manufacturing processes. One of the most significant technological breakthroughs in recent years has been the development and widespread adoption of 3D printing, also known as additive manufacturing. This innovative technology has the potential to revolutionize the way aircraft components and even entire planes are designed, manufactured, and maintained. In this article, we will explore the role of 3D printing in aviation, from the production of individual parts to the assembly of complete aircraft.
Understanding 3D Printing in Aviation
3D printing is a process of creating three-dimensional objects from digital models by adding material layer by layer. This is in contrast to traditional subtractive manufacturing methods, which involve cutting or carving material to create the desired shape. The primary advantage of 3D printing is its ability to produce complex geometries and lightweight structures with minimal material waste, which is particularly important in aviation where weight reduction is crucial for improving fuel efficiency and overall performance.
Advertisement
The 3D printing process typically begins with a computer-aided design (CAD) software, which creates a digital model of the desired object. This model is then converted into a series of cross-sectional layers, which guide the 3D printer in depositing material in the correct pattern. The printer uses a variety of materials, including plastics, metals, and composites, which can be fused together through processes such as melting, sintering, or curing. Once the printing process is complete, the finished object is removed from the printer and post-processing, such as cleaning or finishing, is carried out as needed.
Benefits of 3D Printing in Aviation
There are several key benefits to using 3D printing in the aviation industry, including:
- Reduced weight: As mentioned earlier, 3D printing allows for the creation of lightweight structures with minimal material waste. This can lead to significant weight savings for aircraft, which in turn can reduce fuel consumption and lower emissions.
- Faster production: 3D printing can significantly reduce the time it takes to produce complex parts and components. This is particularly important for the aviation industry, where rapid prototyping and production are essential for maintaining competitiveness and meeting customer demands.
- Customization: 3D printing enables the production of highly customized parts and components, allowing manufacturers to create tailored solutions for specific aircraft models or individual customer requirements.
- Lower costs: By reducing the need for tooling and模具, 3D printing can lower the overall costs associated with the production of aircraft components. Additionally, the reduced waste associated with 3D printing can lead to cost savings in terms of material usage.
- Improved performance: The complex geometries and lightweight structures produced through 3D printing can lead to improved performance in terms of fuel efficiency, speed, and overall aircraft handling.
Applications of 3D Printing in Aviation
The applications of 3D printing in aviation are vast and varied, ranging from the production of individual parts to the assembly of entire aircraft. Some notable examples include:
- Aircraft components: 3D printing has been used to produce a wide range of aircraft components, including engine parts, brackets, and housings. For example, GE Aviation has successfully used 3D printing to produce fuel nozzles for their LEAP engine, which has resulted in a 25% reduction in weight and improved fuel efficiency.
- Customized tools and equipment: Airlines and maintenance organizations are increasingly using 3D printing to create customized tools and equipment tailored to their specific needs. This can lead to improved efficiency and reduced downtime for aircraft maintenance and repairs.
- Aircraft interiors: 3D printing has been used to produce a variety of aircraft interior components, such as seating, armrests, and overhead bins. For example, Airbus has partnered with 3D printing company Materialise to produce customized cabin partitions for their A350 XWB aircraft.
- Entire aircraft: While still in its infancy, there have been some groundbreaking projects that have utilized 3D printing to produce entire aircraft. In 2015, a company calledApis Cor used a large-scale 3D printer to create a small, single-seat aircraft in just three months. More recently, a company called Eviation Aircraft has developed the "Alice" electric aircraft, which features a significant number of 3D printed components.
Challenges and Future Prospects
Despite the numerous benefits and applications of 3D printing in aviation, there are still several challenges that need to be addressed before the technology can be fully embraced by the industry. Some of these challenges include:
- Regulatory approval: The aviation industry is heavily regulated, and any new technology or manufacturing process must meet strict safety and performance standards. Gaining regulatory approval for 3D printed components and aircraft will be a critical step in the widespread adoption of this technology.
- Material limitations: While 3D printing has made significant advancements in recent years, there are still limitations in terms of the materials that can be used and their properties. Further research and development will be needed to expand the range of materials suitable for aviation applications.
- Cost and accessibility: Although 3D printing can reduce costs in some cases, the initial investment in 3D printing equipment and technology can be quite high. As the technology continues to advance and become more accessible, it is expected that costs will decrease, making it more feasible for a broader range of organizations to adopt 3D printing in their operations.
Despite these challenges, the future prospects for 3D printing in aviation are incredibly promising. As the technology continues to advance and become more widely accepted, it is expected that we will see an increasing number of applications in the industry, from the production of individual components to the assembly of entire aircraft. This will not only lead to improved efficiency and cost savings but also pave the way for innovative new designs and capabilities that were previously impossible with traditional manufacturing methods.
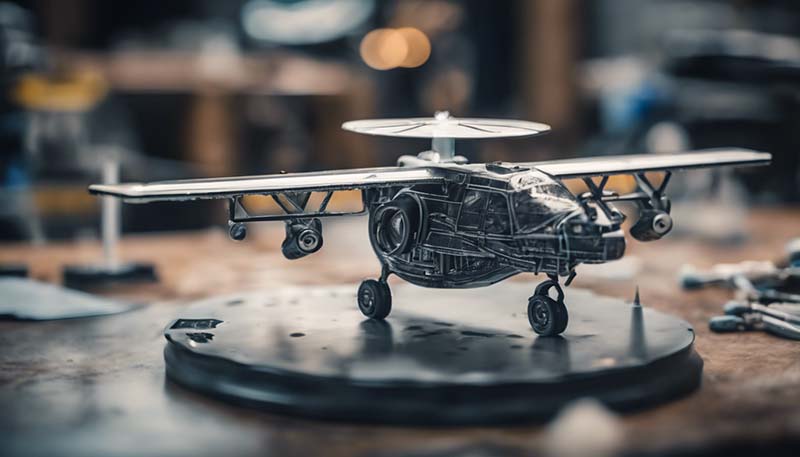
Conclusion
3D printing has the potential to revolutionize the aviation industry by enabling the production of lightweight, efficient, and customized components and aircraft. As the technology continues to advance and overcome the challenges associated with regulatory approval, material limitations, and cost, it is expected that 3D printing will become an increasingly important part of the aviation landscape. From the production of individual parts to the assembly of entire planes, 3D printing is set to play a crucial role in shaping the future of aviation.